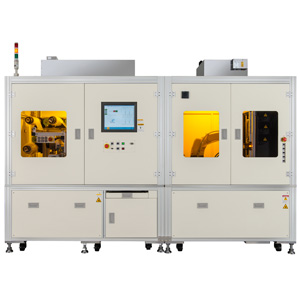
Feature
- SECS ∕ GEM
- Suitable for single ∕ double-sided films
- Fully automatic mounting and laminating (suitable for mounting wafer + ceramic plate ∕ glass)
- The top and bottom plate of the hold-down mechanism are heated to deal with multiple types of film.
Advantages
- Fully automatic rapid production with robot arm
- Lamination in a vacuum environment reduces significantly the residual gases at the laminating interface.
- Loading ∕ Unloading cassette sufficiency
- IR lamp heating function
- Two screens for easy operations.
- Graphic presentation of important statistic data
- User-friendly operation for manual wafer placement
Operation
Take the 6” wafers out of the cassette using the robotic arm. Align the wafer and identify the top and bottom surfaces before placing the wafers on the attachment platform.
Step 1
- Move the attachment platform to the membrane application position. With the pressing roller and membrane clamp pick up the membrane and move the moving carrier to the cutting position.Rotate the cutter to cut the membrane. With the peeling tape, remove the release film from the 6” wafers. Move the moving carrier to the vacuum lamination position.
Step 2
- Take the wafer carriers out of the cassette with the robotic arm. Align the carriers and identify the top and bottom surface before placing the carriers on the attaching disc.Lower the vacuum laminating mechanism to the predefined position and start vacuuming with the vacuuming cover. Start the lamination of the 6” wafers and the carriers as soon as the predetermined vacuum value is reached.
Specifications
Dimensions | 3320 mm × 1100 mm × 2400 mm ( W×D×H ) |
---|---|
Weight | 2500 kg |
AC power | Working Voltage: 415 ( 3 phase ) ∕ 240 ( 1 phase ) Volt. (V)
Plant Safe Current: 60 A |
Air supply | Air Pressure 0.8 MPa
Air Tube Diameter Ø 12 mm |
Object Wafer and Ring
Wafer size | 6″ |
---|---|
Chip size | None |
Laser cut depth | None |
Flat ring size | – |
Tape size | Width 180~250 mm × Length 100 M |
Wafer carrier | 6″ ( Ø 150 mm )、6.5″ ( Ø 165 mm )、8″ ( Ø 200 mm ) |
Features
Vacuum
Lamination in a vacuum environment reduces significantly the residual gases at the laminating interface
IR Lamp
Optional IR lamp for heating depending on process needs
Automatic
Fully automatic rapid production
Adhesive
The adhesive membrane does the job for lamination
Quick Replacement
Quick replacement of membrane and waste material reels
Barcode Reader
For lamination, it can read barcode to record wafer information
Applied Evenly
The laminating pressure is applied evenly
Cut to Fit Shape
For double-sided lamination, the film is cut to fit the required shape at the wafer laminating station according to the outer diameter of the wafer
Aligner Identify
The combination of robotic arm and aligner helps identify the front and rear sides of the wafer and laminating film and flip them over if necessary and the work piece rotates to the correct laminating position automatically
*The information provided here is for reference only. The actual specifications of equipment depend on the equipment requested and delivered.